Cone crushers are powerful machines that grind rock into smaller particles. The crushing chamber is shaped like a cone with a concave bottom, and the mantle rotates eccentrically. Feed level is extremely important, and the material must be evenly distributed throughout the machine. For best results, feed level must be maintained throughout the entire crushing process. This is called the Symons Brothers principle. Cone crushers can be used for a variety of applications, and they are typically paired with a feeder.
Concave cone crusher
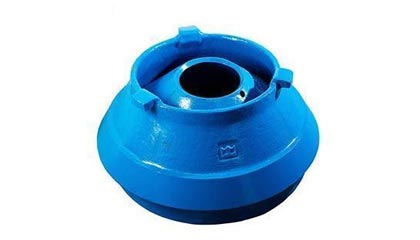
A cone crusher is a machine that crushes raw materials into smaller pieces. This type of crusher has two parts: a stationary bowl and a concave. The mantle, or part of the crusher, is a steel sleeve that rotates inside the cone. As the raw material passes through the cone, it is crushed by the force of the rotating mantle. As the material passes through, the gap between the bowl and mantle decreases, and the broken material travels down the cone. The gap setting can be adjusted according to the size of the finished product.
Telsmith manufactures the Titan line of cone crushers. These machines offer 840 tons of throughput per hour and are compatible with the Trac10 automation system. The machine’s strong main frame and high power transmission rate make it suitable for most crushing operations. Its high capacity lubrication system, hydraulic adjustment, and grease seal ensure maximum productivity. The SP Cone Crusher has an increased stroke and eccentric height, increasing the crushing ratio and efficiency.
Mantle rotates eccentrically
A cone crusher is a crushing device wherein the mantle rotates eccentrically. This eccentric motion causes the gap between the mantle and concave to move from the narrow setting to the widest setting. This movement increases the crushing force. The mantle is a fixed ring inside the upper casing of the crusher. The mantle and concave form the working surfaces, Check out this site.
The mantle and head 14 rotate eccentrically about axis 18 for crushing. The distance between the mantle and bowl liner causes the annular space 62 to vary. The rotating mantle impacts the large particles and compresses them to form a final product. The mantle and bowl liner act together to reduce the size of the aggregates. These two elements work together to break the aggregate into desired sizes.
Feed level should be consistent
When feeding rock into a cone crusher, the feed level should remain consistent. Too much or too little can lead to problems and unexpected production costs. The following tips will help keep your feed level constant. The following are some important tips for maintaining the feed level of cone crushers:
The material should be positioned in the hopper at the same level, so that the product particle size is consistent. Often, the feed material is not level and causes problems. Inconsistent feed level leads to uneven product size and reduced throughput tonnage. Moreover, uneven feed can lead to elongated or flat product particles. This can also lead to production losses. Thus, feed level should be consistent in cone crushers.
Symons Brothers principle
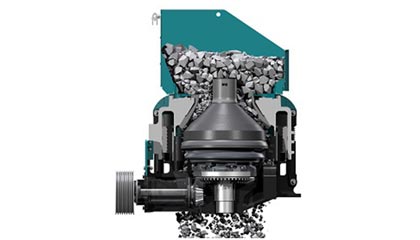
A Symons Brothers cone crusher works by directing a motor through an eccentric sleeve to the crushing chamber. The crushing chamber is an annular cavity, and the cone continuously crushes the materials. The cone is composed of a fixed cone and a moving cone. The moving cone is protected from abrasion by a cover, and the fixed cone can be adjusted to the desired setting for a specific application.
The crushing action is achieved through a combination of oscillation and throwing. The crusher consists of a concave liner mounted on the main shaft and a moving mantle liner within the upper casing. These two components are arranged in such a way that their individual parts provide the crushing action. They have the potential to produce high yields. This lowers the overall cost per ton of finished product.