The future of PCD tooling is bright, especially as the technology continues to improve. High spindle speeds and precision edges are just a few benefits of PCD tooling. Its flexibility and cost efficiency make it a smart choice for different workers with different needs and budgets. Read on to learn more about PCD tooling. You’ll be amazed at how quickly the industry is evolving. And you’ll also be glad that you’re not the only one embracing this technology.
Durability
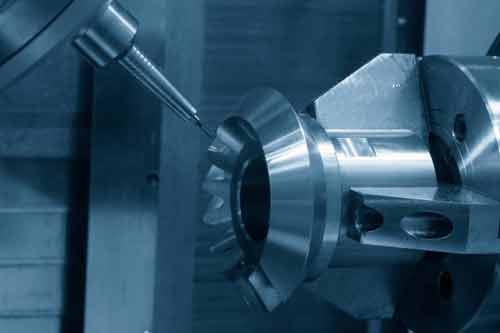
The morphology of flank wear of PCD tools was investigated using EDS mapping. In general, the flank faces were eroded sequentially during the machining process. The temperature and the tool/workpiece contact load were highest near the tip of the tools. Therefore, this structure was unable to withstand long-term use. The consolidated layer was largely removed during the cutting process. However, the flank face of 002E was preserved due to its thicker adhesion.
Another advantage of PCD tooling is its abrasion resistance. Depending on the application, PCD cutting tools can last up to 50 times longer than conventional tools. They are an excellent choice for machining wear resistant non-ferrous materials, like copper. Other materials that PCD is suitable for include composite materials, fiberglass, and green ceramics. This material will also significantly reduce surface roughness. The high-performance characteristics of PCD tools make them a popular choice for the machining of complex materials.
Precision edges
Surface finishing is a key step for metal producers, and the use of traditional techniques can be costly and time-consuming. However, PCD tooling offers greater precision than traditional methods, and can also produce smoother, more accurate edges and dimensional measurements. Moreover, PCD-based solutions eliminate the need for secondary finishing techniques, saving time and money. PCD tooling is also capable of producing higher feed rates, a key benefit for manufacturers.
Another benefit of PCD tooling is its great efficiency. It can run up to ten times faster than traditional tools, enabling users to finish more components in less time without compromising on quality. Furthermore, PCD tools can withstand a high amount of wear and tear, allowing them to deliver optimal performance for longer periods of time. Furthermore, they are extremely durable, allowing users to work more efficiently while ensuring flawless surfaces.
High spindle speeds
One common question that comes up when analyzing the performance of a PCD cutting tool is whether high spindle speeds are necessary for effective metal removal. The answer is both yes and no. The reason for this is that high spindle speeds increase the rate of metal removal and decrease the limit depth of cut. Both questions are relevant for milling a wide range of materials, from titanium to steel. However, in many cases the maximum spindle speeds can be too high for the materials.
To determine the right speed for your cutting process, start by evaluating your machine’s maximum spindle speed. The maximum spindle speed is your ceiling speed, but you can increase this figure by changing your cutting tool. Higher-quality tooling allows higher speeds, and new technology has made it possible to achieve previously unimaginable cutting speeds. If you are running a high-speed machining process, you can boost the speed of the machine by changing the cutting tool.
Cost
The cost of PCD tooling seems high compared to carbide tooling. However, it pays for itself quickly. The most common uses for PCD tooling include the machining of abrasive materials, composite materials, and workflows involving high volume. Below, you’ll learn how to reduce the cost of PCD tooling. Here are some reasons why. Hopefully, you’ll find this article informative.
Conclusion:
A primary advantage of PCD tooling is the durability of the cutting tools. Because these tools do not corrode, they will last a long time. Additionally, the tool will not need to be sharpened as often as carbide tools. These benefits may help offset the increased cost of PCD tooling. But the real benefits of PCD tooling far outweigh the extra cost. They can last up to a hundred times longer than carbide tools and require less downtime.